How Industrial Gearbox Manufacturers Ensure Compatibility With Existing Systems
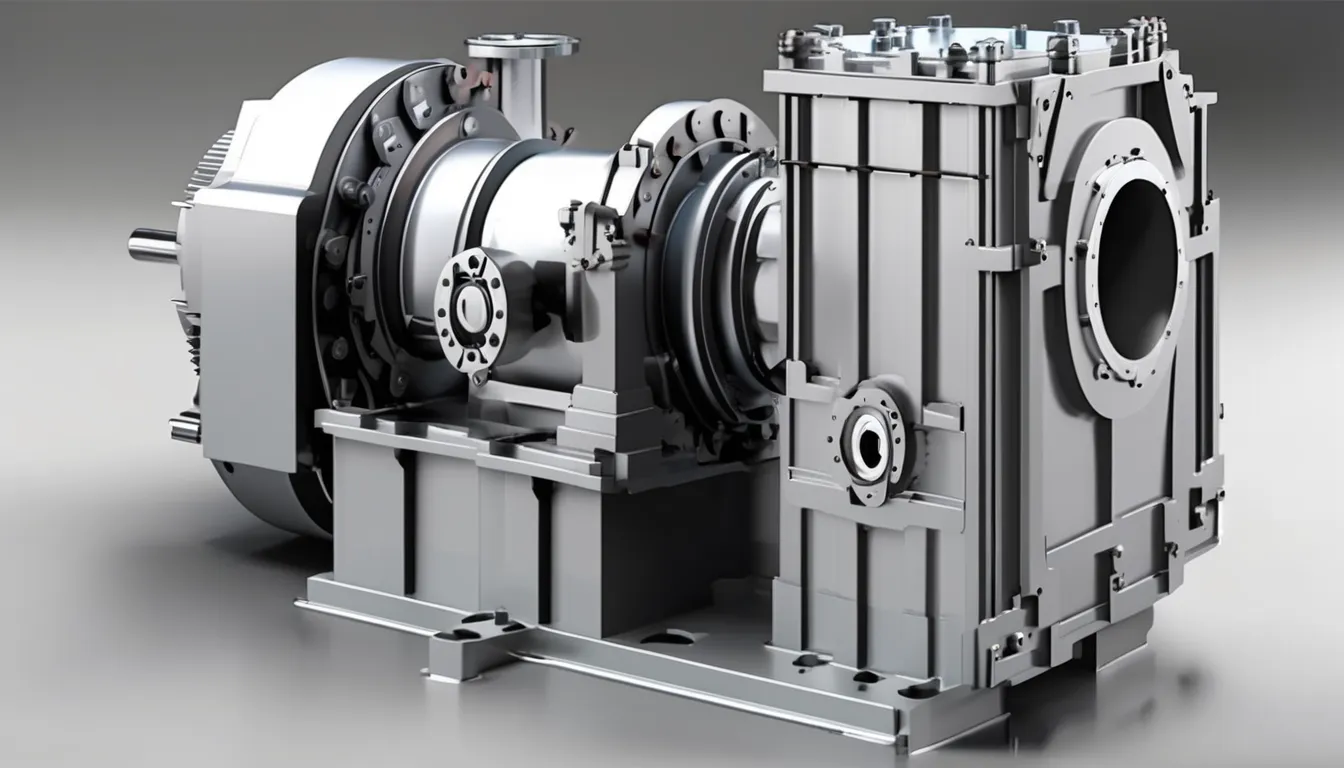
When you think about industrial gearboxes, compatibility with existing systems is crucial, isn’t it? Manufacturers focus on established standards and specifications, like those from ISO and AGMA, to ensure their products fit seamlessly into your operations. They assess factors such as input/output speeds and torque, but that’s just the beginning. What happens during the testing and validation processes can make all the difference in performance and reliability. Understanding these aspects could change how you approach your next equipment upgrade—let’s explore what that entails.
Understanding System Compatibility
When selecting an industrial gearbox, understanding system compatibility is crucial to ensuring optimal performance. You need to consider how the gearbox will interact with your existing machinery, as mismatches can lead to inefficiencies or even equipment failure.
Start by examining the specifications of your current system—this includes input and output speeds, torque requirements, and the physical dimensions of the space where the gearbox will fit.
Next, evaluate the type of application you’ll be using the gearbox for. Different applications may require varying levels of durability and load capacity, so make sure the gearbox can handle the demands of your specific task.
Additionally, pay attention to the mounting options; compatibility in this area can save you time and cost during installation.
Don’t forget to consider the lubrication method as well. Some gearboxes require specific lubricants to function efficiently, and using the wrong type can lead to increased wear and tear.
By thoroughly assessing these compatibility factors, you’ll increase the likelihood of a successful integration, enhancing the longevity and reliability of your equipment.
Ultimately, taking the time to understand system compatibility pays off in the long run.
Design and Engineering Techniques
Selecting the right design and engineering techniques for your industrial gearbox can significantly impact its performance and longevity. To ensure optimal functionality, you’ll want to consider various factors, including material selection, gear geometry, and manufacturing processes. Each of these elements plays a crucial role in how well your gearbox integrates with existing systems.
Here’s a breakdown of essential design and engineering techniques:
Technique | Description | Benefits |
---|---|---|
Finite Element Analysis (FEA) | Simulates physical behavior under load | Identifies potential failures early |
Gear Tooth Design | Optimizes shape and size of gear teeth | Reduces wear and improves efficiency |
Material Selection | Chooses appropriate materials for durability | Enhances performance and lifespan |
Tolerance Control | Maintains precision in manufacturing | Ensures compatibility and reduces backlash |
Surface Treatment | Applies coatings or treatments for wear resistance | Extends service life and reliability |
Standardization and Specifications
In the realm of industrial gearboxes, standardization and specifications play a crucial role in ensuring compatibility across different systems and applications. When you’re selecting a gearbox, you’ll encounter various standards set by organizations like ISO and AGMA, which provide guidelines on dimensions, performance, and materials.
Adhering to these standards not only simplifies the selection process but also enhances interoperability between components. You’ll find that established specifications help manufacturers align their products with industry requirements. By conforming to these norms, you’re reducing the risk of incompatibility issues that can arise during installation or operation.
This consistency allows you to mix and match components from different manufacturers without worrying about performance discrepancies. Moreover, standardized gearboxes can streamline maintenance and replacement processes, saving you time and resources.
When you need to replace a worn-out gearbox, you can easily find a compatible unit that meets the same specifications, ensuring your system remains operational.
Testing and Validation Processes
Testing and validation processes are essential to ensure that industrial gearboxes meet the required performance and reliability standards.
You’ll find that manufacturers typically begin with rigorous design verification tests. These tests assess structural integrity, load capacity, and efficiency to confirm that the industrial gearbox manufacturer performs as expected under various conditions.
Next, manufacturers conduct functional testing, where they simulate real-world applications. This step helps them identify any potential issues that could arise during operation.
You might be interested to know that these tests often include thermal and vibration analyses, ensuring that the gearbox can withstand the stresses of continuous use.
Once the initial tests are complete, manufacturers validate the gearbox against industry standards. This involves comparing the gearbox performance with established benchmarks to guarantee compatibility with existing systems.
You should also look for certifications from recognized industry organizations, as they indicate adherence to safety and quality guidelines.
Ongoing Support and Maintenance
Ongoing support and maintenance are crucial for maximizing the lifespan and efficiency of industrial gearboxes. When you invest in a gearbox, you want it to perform optimally for years to come.
Regular check-ups and maintenance can prevent costly breakdowns and extend the life of your equipment.
Make sure you focus on the following aspects:
- Timely servicing: Routine inspections can catch issues before they escalate, saving you time and money.
- Expert advice: Access to specialized knowledge helps you make informed decisions, ensuring you’re using the best practices for maintenance.
- Emergency support: Knowing you have reliable assistance during unexpected failures provides peace of mind.
Conclusion
In conclusion, when you choose an industrial gearbox manufacturer, you’re ensuring that your systems work smoothly together. By focusing on compatibility through precise design techniques, adherence to standards, and thorough testing, these manufacturers help you avoid issues down the line. Plus, with ongoing support and maintenance, you can feel confident in the longevity and performance of your equipment. So, investing in a reliable gearbox not only meets your current needs but also sets you up for future success.